Table of Contents
- What Are Hydraulic Dock Levelers?
- How Hydraulic Dock Levelers Work
- Hydraulic vs. Mechanical & Air Levelers
- Key Features and Specs to Consider
- Types of Hydraulic Dock Levelers
- Standard Loading Dock Leveler
- Hydraulic Dock Systems
- Heavy Capacity Dock Leveler
- Hydraulic Loading Dock Ramp
- Tall Dock Leveler
- Safety and Compliance
- Installation and Maintenance
- Use Cases and Industry Applications
- Buying Considerations and Checklist
- Conclusion
The Complete Buyer’s Guide to Hydraulic Dock Levelers: Features, Specs, and Use Cases
Welcome to the ultimate guide on Hydraulic Dock Levelers – the heavy duty bridges that make warehouse loading and unloading smooth sailing instead of a bumpy road. Think of a hydraulic dock leveler as an automated, motorized ramp: it raises, lowers, and extends a hinged lip to safely connect a loading dock to a truck bed. This alleviates awkward height differences and eliminates the need to manually haul dock plates around (no more muscle-tugging against gravity). Hydraulic systems control both the platform deck and the lip with electric pumps and cylinders, so dock workers just press a button and voilà, the dock leveler does the heavy lifting. In short, hydraulic levelers are like the tech savvy, user-friendly relatives of the old school scissor or chain pull levelers built to handle massive loads while keeping operators out of harm’s way.
What Are Hydraulic Dock Levelers?
A hydraulic dock leveler is essentially a power operated, hinged ramp installed between a loading dock and a truck trailer. It vertically adjusts to various truck heights, creating a smooth transition so forklifts and pallet jacks can roll on and off safely. In plain English, it’s like having an automatic bridge that adapts to every delivery truck. The heavy steel deck spans the gap, and an integral lip (usually 16–20 inches long) folds out onto the trailer bed. Hydraulic cylinders powered by an electric motor and pump do the heavy lifting (literally). This all in one system replaces manual methods (like setting a dock plate) with a push button solution, reducing labor and risk of injury.
Hydraulic levelers come in many sizes and weight capacities. For example, Beacon’s [Loading Dock Leveler] BH5 series spans 6–7 feet wide and 6–10 feet long, and can handle 25,000 to 45,000 lb. loads. The platform is built of welded steel with a slip resistant diamond tread surface, and full length toe guards protect feet along the edges. In contrast, [Heavy Capacity Dock Levelers] can carry up to 80,000 lb. for forklifts carrying super heavy goods. All hydraulic levelers have safety measures like side toe guards and velocity fuses (to prevent free fall if hydraulic pressure is lost), making them ideal for demanding, high-traffic docks.
How Hydraulic Dock Levelers Work
Operating a hydraulic leveler is straightforward. The operator presses a button (mounted nearby or via a control panel) and the built in pump drives hydraulic fluid into cylinders. These cylinders lift the deck while a second cylinder extends the hinged lip out onto the truck bed. As soon as the truck moves away, sensors or built in timers trigger an auto-recycle function: the lip retracts and the deck lowers back to stored position. This “set it and forget it” automation means the deck resets itself every time a trailer leaves, saving time and preventing forgetting to retract the lip.
Behind the scenes, the hydraulic system offers gentle, adjustable operation. Unlike a mechanical (chain-pull) dock leveler that can snap down if not handled carefully, hydraulics typically include flow control valves or velocity fuses. These devices act like shock absorbers: if a hydraulic line leaks or breaks, the fuse locks and prevents the deck from free falling. In other words, hydraulic levelers trade manual grunt work for smooth, controlled movement, giving warehouse teams a bit of keyboard “zen mode” instead of grappling with big metal ramps.
Hydraulic vs. Mechanical & Air Levelers
It’s worth contrasting hydraulic levelers with the other main types: mechanical (spring/chain) and air-powered. Mechanical levelers use springs or cams and a pull chain to raise the deck; they are simple and cost effective, but require manual effort and have no powered assist. Air powered levelers use an air bladder to lift the deck.
Ease of Use: Hydraulic requires only a button press, so fewer injuries from heavy pulling or “falling on the deck”. Mechanical often means bending and pulling heavy chains.
- Adjustability: Hydraulics can auto adjust under load if the trailer bed “floats” due to air-ride suspension, whereas mechanical systems rely on carefully balanced springs.
- Capacity: Hydraulics readily scale up for very heavy loads (50k–80k+ lbs.), while mechanical springs become huge and unwieldy at those levels.
- Maintenance: Hydraulic systems do require periodic checking of pumps and hoses. Mechanical levelers have more mechanical wear (springs, cables) but simpler tech.
In general, if your operation involves frequent truck changes and heavy forklifts (think distribution centers or busy factories), a hydraulic leveler pays off by boosting safety and uptime.
Hydraulic levelers offer a significant advantage in terms of automation, safety, and load capacity. Here’s how they compare:
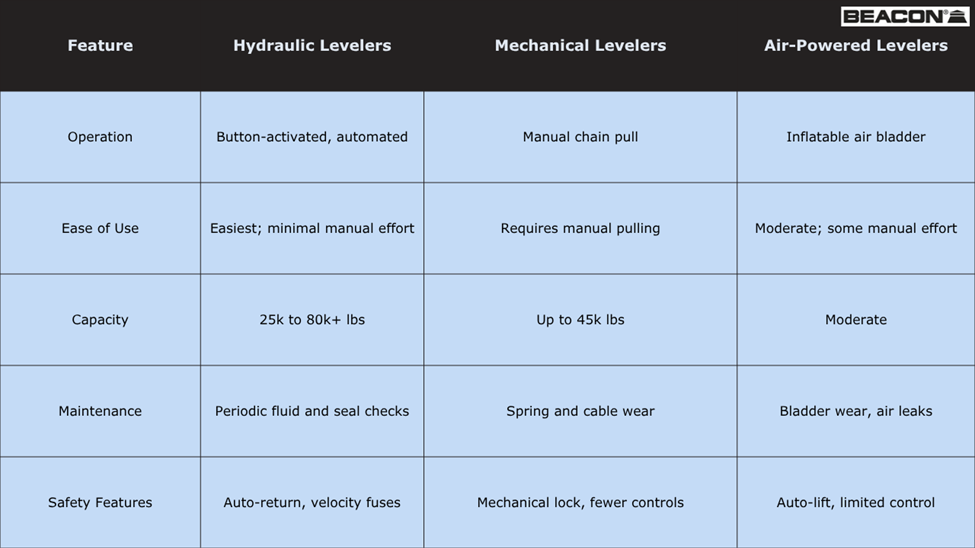
Alt: Feature comparison of Hydraulic Levelers, Mechanical Levelers and Air Powered Levelers.
If your operation includes frequent truck loading and unloading with heavy cargo, a hydraulic system is the most efficient, durable, and operator-friendly solution.
Key Features and Specs to Consider
When shopping for a hydraulic dock leveler, several key specifications should match your needs:
- Load Capacity: Rated in pounds. Standard hydraulic levelers handle 25k–45k lbs. of dynamic weight. Heavy duty models go to 60k or 80k lbs. Remember, “published rating” is usually static capacity; dynamic or rolling capacity is often 50% of that. (So a 50,000 lb static deck may be rated ~25,000 lb dynamic for a moving forklift.) Always choose a safety margin above your heaviest load.
- Deck Size: Common deck widths are 6′, 6.5′, or 7′ (72″, 78″, 84″). Lengths run 6’–10′ (some ramps up to 12). Larger widths accommodate wider forklifts. Deck thickness (usually 3/8, 1/2″ or 5/8” or more) and internal support (beams, gussets) determine strength.
- Lip Length: Standard lip is 16″ (to rest firmly on the trailer bed). Longer 18″ or 20″ lips are optional, especially for trailers with gaps or double-lip requirements. (Heavy Capacity models often have the full 16″ hinged lip standard) The longer the lip, the smoother the transition, but also the more deck space needed when parked.
- Hydraulic Power: Motor specs vary (e.g, 1 HP, 230VAC 1Ph is common). If you’re in a high cycle environment, high-pressure pumps, and quality seals. Beacon units, for example, include a sealed pump/motor with a manual lowering valve for power loss.
- Control System: Beacon offers touch screens, wall mounted pushbutton stations, or optional rotary selector switches.
- Safety Accessories: Full range toe guards on sides to prevent foot injuries; edge of dock bumpers; integrated velocity fuses in the hydraulic cylinders to stop sudden drops; and dock lighting.
Here’s a quick bullet list of typical product features (example based on Beacon BH5 series):
- Construction: Heavy-duty welded steel, typically with a robust rear frame support and gussets.
- Finish: Enamel gray paint with yellow markings on edges. A Few options include skid resistant deck coating or weather seals.
- Operation: Electric motor, pump, and two hydraulic cylinders (one for deck lift, one for lip). Auto-return (auto recycle) to the stored position standard.
- Range of Motion: Typical travel is ±12″ from dock level (some longer levelers have more travel). Dock ramps might allow 12″ above and 12″ below dock for extreme height changes.
- Controls: Touch Screen as strandard.
- Warranty: Look for 5 year structural and 1 year cylinder and parts warranties.
Real-World Example: A mid-sized warehouse might pick a 30,000 lb, 72″×8′ dock leveler with a 16″ lip. That covers most standard semi trailers, forklifts, and double stacked pallets. If their operations include heavy manufacturing or extra heavy equipment, they’d consider a [Heavy Capacity Dock Leveler] up to 80,000 lbs.
Types of Hydraulic Dock Levelers
Not all hydraulic levelers are one size fits-all. Various models target specific dock situations. Below are common categories (each linked to Beacon’s product info for details):
BH5 Loading Dock Leveler
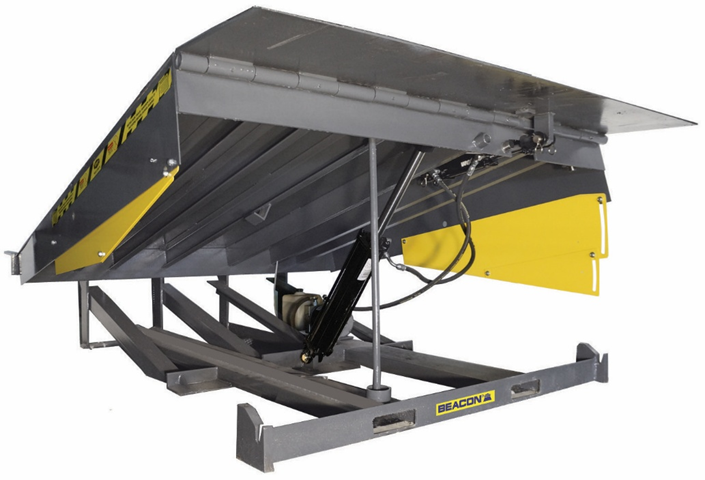
These are the workhorses for typical docks. The Beacon BH5 series (see Loading Dock Leveler) is a great example: 6–7 foot wide decks, 25k–45k lb capacity, 1 HP motor, and a 16″ hinged lip. They include full-length toe guards and bumpers. Ideal for general distribution centers, warehouses, and factories. Most warehouses will have these installed at each bay.
Hydraulic Dock Systems
These are similar to standard levelers but often emphasize cost-effectiveness for high-volume use. Beacon’s BH2 series (Hydraulic Dock Systems) has 25k–45k lb capacity and 6–8 ft deck sizes. They’re “push-button” pit levelers built for rigorous duty. In practice, you’d use a hydraulic dock system in a busy multi-bay dock where you need simple, reliable performance without the extra bells.
Heavy Capacity Dock Leveler
For industrial sites handling enormous loads (think 50k–80k lb forklifts or oversized vehicles), heavy-duty models are the answer. Beacon’s BHD5 series (see Heavy Capacity Dock Leveler) supports 50k, 60k, and 80k lb static capacity. It has a beefed-up structure – thicker steel, extra support angles, and an auto-recycle feature. These units are built for multi-shift, rugged operations. If you see giant military trucks, railcars, or large construction equipment being loaded, a heavy-capacity leveler is probably at work.
Hydraulic Loading Dock Ramp
This is a special long ramp (up to 12’ nominal) on dual lift cylinders. Picture a slanted bridge for unusual dock heights or low docks. The Beacon BEH5 ramp lifts 12″ above or below the dock, allowing forklifts to climb in and out on a gentle slope. Use cases include very low docks that need an extra-long lip or compensating for high container bottoms. Essentially, it’s a hydraulic yard ramp that’s built into the dock.
Tall Dock Leveler
These are custom units for deep pits (24″–50″ tall) where conventional levelers won’t reach the truck bed. The HPK-BEH series can be made for pits where older docks left an unusually high pit floor. If you’re renovating an old building a Tall Dock Leveler ensures you don’t have to rebuild the pit it simply extends farther downward. Capacities here are usually around 20k–30k lb.
Tip: Don’t confuse these with “edge of dock” levelers (small dock plates) or scissor lifts – those are different categories. Our focus here is on pit-style hydraulic levelers (permanently installed, recessed into a pit).
Safety and Compliance
Safety is paramount at any loading dock. Forklift trucks and human legs on a raised dock leveler can spell disaster without proper precautions. Fortunately, hydraulic levelers are designed with safety in mind.
- Edge Protection: Beacon’s units, for example, include full-range toe guards to keep feet and wheels away from pinch points. Always keep these guards in place during operation.
- Vehicle Restraint and Chocks: Even with a leveler in place, the trailer could creep away. Modern docks often use light-activated restraints. Always secure the truck before walking on the leveler.
- Operator Training: Only trained personnel should operate forklifts and levelers. notes that falls from a loading dock in a forklift can be fatal, emphasizing that docking areas are inherently hazardous. Training includes inspecting the leveler first for damage or obstructions.
- Safe Work Practices: “Use dock leveler plates to provide a stable surface to move materials and prevent falls. Ensure dock plates are level with the dock surface when loading is complete.”
- Signage and Markings: Bright safety yellow paint on edges and clear warning signs (ANSI Z535 style) improve visibility. Beacon suggests adding yellow/black striping on toe guards.
- Emergency Stop: If a person or object gets pinched, the power should be cut out. Optional E-stop button is available.
By designing with these safety features and following best practices, hydraulic levelers become much safer. They automate the lift so operators don’t need to climb under or manually prop heavy ramps – a big ergonomic win.
Also, check out this Loading Dock Safety Guide by Environmental Health & Safety.
Installation and Maintenance
Installation: Hydraulic levelers are usually recessed into a concrete pit. The pit depth is typically equal to the dock height, plus a few inches. Position the leveler so that when it’s lowered, its deck is flush with the dock floor. Anchoring bolts and pit curbs must be precisely placed (follow manufacturer templates). Electrical wiring conduit is (for the motor). Beacon provides detailed pit dimensions.
Maintenance: Regular upkeep is crucial for reliability. Key tasks include:
- Check hydraulic fluid level and add oil as needed (usually a non-foaming hydraulic oil). Change the fluid per the manufacturer’s schedule.
- Inspect hoses and cylinders for leaks or cracks. Replace any damaged seals.
- Lubricate pivot points on the lip hinge and deck fulcrum.
- Test safety features: toe guards should move freely; limit switches (if any) should cut power; emergency stop should function.
- Keep the pit clean – debris in the pit can obstruct movement or damage the deck. The ramp profile of the deck can accumulate dirt; sweep it regularly.
- Verify control wiring and buttons are in good condition. Replace frayed cables or cracked switches.
- Test the auto-recycle function on each delivery: ensure the deck lifts and lowers fully and that the lip retracts automatically.
A typical maintenance schedule is quarterly inspections and an annual service by a trained technician. During these checks, you may recalibrate the “stop points” where the lip begins to lower, and adjust spring tension (if any counter-balance springs are present). Some facilities also have a dry test (running the leveler without a load) to listen for unusual noises or sluggish operation.
By keeping up with service, you’ll avoid surprises like sudden drops or stuck lips. As Beacon notes for heavy units: “Heavier capacity units will not only accommodate heavier loads but will last longer in multi-shift operations.” Proper maintenance extends that lifespan.
Use Cases and Industry Applications
Hydraulic dock levelers are ubiquitous in industries where large shipments are routine. Here are common applications:
- Distribution Centers & Warehouses: These facilities run forklift fleets day and night. Trucks back up in rotation, often with minimal staging time. Hydraulics allow one operator to cycle multiple trailers quickly. As Beacon explains, these levelers are “ideal for busy loading areas that require durable and dependable performance. Trusted by leading industries, our hydraulic dock levelers are commonly installed at distribution centers, manufacturing facilities, warehouses, airports, and assembly plants.”
- Manufacturing Plants: Factories receiving raw materials or shipping heavy finished goods need levelers that handle repeated use. For example, an auto plant might offload frames or engines on heavy forklifts – here, heavy-capacity levelers shine. The “smooth and efficient cargo transfer” touted by Beacon helps prevent jolts that could spill parts or injure workers.
- Cold Storage & Refrigerated Trucks: In cold environments, hydraulic fluids and metal contracts differently. High-quality levelers (with cold-weather fluids and seals) are vital. The Hydraulic Loading Dock Ramp is often used for refrigerated trucks: because their beds sit lower (empty), the extra-long ramp and travel range keeps forklift angles safe.
- High-Security / Government Facilities: Military bases and prisons might have securely docked bay doors. Hydraulic levelers integrate well with security protocols – for instance, they can be configured to only activate when a correct access code or truck restraint is engaged. Beacon’s option for a combined Versa panel (leveler, restraint, door) exemplifies this coordination.
- Retail Distribution: Even big box retailers use hydraulic levelers behind the scenes. Imagine a home improvement store receiving pallet loads of appliances levelers ensure hand trucks and forklifts roll in smoothly without damaging floors.
Example Analogy: Think of a hydraulic dock leveler as a ramp for cargo: it moves heavy loads between two fixed points (dock and trailer) safely and easily. Without it, the alternative is like trying to load a moving target by hand.
Buying Considerations and Checklist
When selecting a hydraulic dock leveler, keep a checklist of your facility’s needs:
- Truck Fleet & Dock Height: Are your trucks mostly 48-ft, 53-ft, or a mix? Are trailers “air ride” (which float up/down)? If so, an auto recycle hydraulic model is helpful. Also note dock height: if unusually high or low, that will affect pit depth or ramp requirements.
- Load Profile: What’s the heaviest load (with forklift) you’ll ever carry? What does the traffic volume look like? High cycle (many trucks per hour) demands a robust build and possibly faster cycle speeds.
- Pit Dimensions: Measure your existing pit (depth, width). If no pit exists, you’ll need construction. Some levelers (like Tall Dock Levelers) can be used for old non standard pits.
- Power Availability: Confirm electrical service at the dock is 115V/230V, single phase. Beacon BH5 can work on 1-Phase 115V; optional 230V or 460V three-phase is available.
- Safety Requirements: Ensure the leveler has the needed toe guards and fuses. Vehicle restraint systems help prevent premature pull away.
- Budget and ROI: Hydraulic units cost more upfront than simple mechanical plates, but they improve throughput and reduce injury risk. As one vendor notes, “while mechanical levelers are cheaper initially, you may pay more in maintenance costs over 10 years compared to hydraulics,”. In other words, a slightly higher capex can mean long-term savings and efficiency.
- Vendor Support: Look for a supplier that provides documentation (installation diagrams, maintenance manuals) and tech support. Beacon’s product pages include tech sheets and an owner’s manual, which are useful.
Checklist:
- Capacity ≥ expected load (plus safety buffer).
- Deck width and length to match forklift and dock door dimensions.
- Lip length (16″, optional 18/20″).
- Control panel type (touch screen, basic push-button or advanced controls).
- Required safety accessories (retaining pins, straps, etc.).
- Warranty length (3–5 years recommended).
- Installation services (will you hire an electrician/contractor?).
Conclusion
Hydraulic dock levelers are an essential investment for any busy warehouse or loading dock. They blend heavy duty performance with automated convenience, turning a risky gap between dock and truck into an easy ramp. By understanding features (capacity, size, lip), types (standard, heavy capacity, ramps, tall models), and safety needs, you can select the right leveler for your operation. Whether your dock handles tons of freight every hour or occasional deliveries, a hydraulic leveler enhances throughput and safety. Remember that “the best dock leveler will check all the boxes” – fitting your budget, lasting for years, and keeping everyone safe. In practical terms, that means choosing the right specs, maintaining it well, and training your team on safe use.
In the end, hydraulic dock levelers quietly keep your facility running, like a backstage crew changing sets in a play. They handle the heavy lifting so your warehouse orchestra can perform without missing a beat.